Normally when you talk to someone in the engineering, maintenance or reliability fields about the subject of better productivity, their minds usually jump to ways to increase the productivity of what they are working on - better throughput in the factory, increased wrench time, decreased down time, etc.
So when do we stop and think about how we can make ourselves more productive?
Getting Things Done
I've been using David Allen's Getting Things Done(GTD) methodology for some time. For those who haven't heard, GTD is a framework on how to better manage the task and work you need to get completed. The framework has five basic steps:
- Capture - collect all of your to do's, projects, action items, etc.
- Clarify - is what I have collected actionable, and if it is, decide if I need to do it now, defer it to later, delegate it someone else, or drop it completely.
- Organize - put things in their proper place.
- Reflect - look over your lists and determine what to do next.
- Engage - go out and do what you now believe needs to get done.
But when I looked at these 5 steps, I saw at a broad level everything a maintenance department should be doing fit in GTD's workflow.
- Capture - collect all the work that needs to be done in Maximo.
- Clarify - think about a job and is it something that needs to be done today or tomorrow, should it get pushed back to next week, should we hire a contractor to do the work, or is the job out of date and get dropped.
- Organize - get the list of jobs we're going to do on to the schedule.
- Reflect - review the schedule with Production and make sure what we believe needs to get done, should get done.
- Engage - issue work to mechanics and technicians so the tasks get completed.
But then I started to think about the collateral responsibilities most of us have in our organizations. We have tasks that go beyond issuing work orders and running reports. I started to think about ways I could GTD to help make me and my department more productive.
Keep running lists of meeting agendas
Most organizations will have a regular team meeting related to reliability and maintenance. The agenda for these meetings are posted before the meeting and some ideas on the next meeting are written down somewhere too. This is then repeated month after month through out the year.
Assuming you're having a monthly team meeting, a better approach is to create 12 agenda files (Word, Excel, text file, etc) for all the upcoming meetings. This way as new agenda ideas come up, you can capture them immediately in that month's agenda or see that the agenda for 2 months from now is already pretty full.
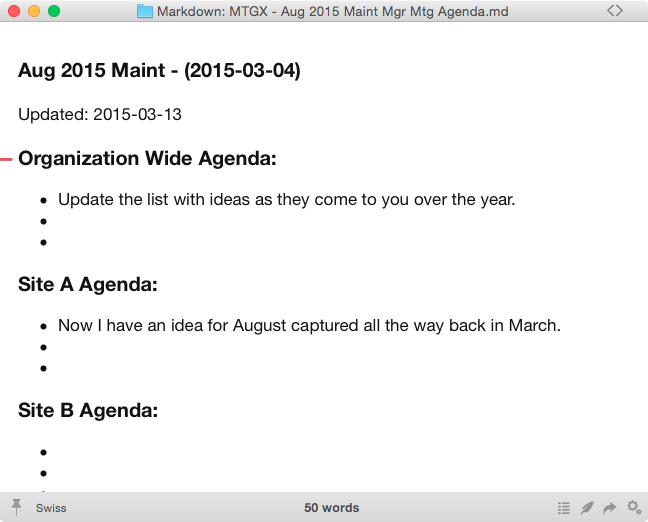
Now I'm collecting ideas for August all the way back in March.
Treat all maintenance activities with one inbox
Let's not lie to each other. Most organizations will treat their maintenance groups as an ad hoc project group at times. The work being isn't truly corrective maintenance, it's more like enhancement maintenance. But when reviewing the workload and priorities of these project tasks, they will sometimes get put on a spreadsheet or email list.
Definitely not the way we should be managing these tasks.
Put all of the tasks onto individual work orders (we want to track and time & materials anyway) and then use a simple BIRT report to keep track of all the projects. So as new work comes up and old work drops off, the processes we already use to manage work orders will manage the project list too. As project priorities change, change the priority value on the work order to reflect its importance.
Do less work trying to get work done
I have to admit, I've been doing something close to this, but George Williams, from Bristol Myers Squibb, did a great job at Interconnect 2015 of connecting the dots on how to use BIRT reporting in Maximo to help employees focus what needs to get done. They used a three staged linked report to show their employees what needed their attention versus having them work on finding what needed their attention.
The process was pretty simple:
- An over view report to show what needed to be looked at.
- A list to report to quickly scan what was being looked at.
- A detail (print) report to assign work to employee to get completed
Aging Report → List Report → Details Report
The first report is a summary aging report that shows transactional records (work order, purchase request, purchase order, etc) in a grid based on data type vs age:
| | WO Age |||||
| WO Type | 0-30d | 30-60d | 60-90d | 90d+ |
|:------------:|:-----------:|:-------------------:|:---------------:|:------------:|
| PM | 12 | 23 | 2 | 1 |
| CM | 23 | 18 | 4 | 6 |
| EM | 14 | 34 | 0 | 3 |
Each of the work order aging counts would link to a work order list report. Then the work order list report would link to the WO print report. This allowed the maintenance department to identify outlier activities that needed to be monitored.
The report is placed on a Maximo user's Start Center, so they won't have to work at getting the information they need. It was one of the best presentations I saw at Interconnect.