Over the years I've learned to pick up ideas and advice from wherever I can find it. I recently came across a tweet from @ThePracticalDev on the obligation of a software developer. The article was originally written by Stelios Voskos (@steliosvs91) on the 5 rules a developer should follow.
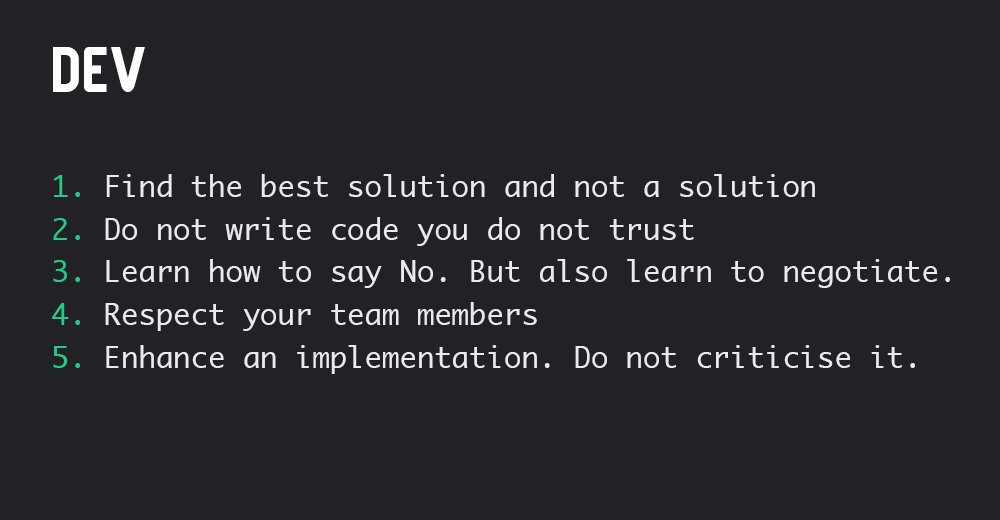
What struck me funny was these were the same types of rules anyone concerned about their plant reliability should focus on as well. Here's how I took these 5 rules and applied them to maintenance and reliability.
1. Find the best solution and not a solution
This should be a universal mandate for anyone that works in reliability, maintenance or engineering. How many times have walked into a situation to hear, "Well Bob took a look at this yesterday and said he fixed it." 1 We all have a lot of pressure from Operations to fix whatever is wrong and get the plant running again. What we fall short of doing most of the time is to look at the situation and work towards a solution to repair the problem. Using bailing wire and duct tape, why effective when you have no other choice, is not the best solution to address problems in our plants. Alway try to bring options to the table the looks at the long term benefits to the equipment and the company.
2. Do not write code you do not trust
Most of us in the maintenance and reliability areas don't write code.2 While we might not write code, we do have people in our groups that write the equivalent to code - job plans. Computer code is just a set of instructions to carry out specific tasks. The same can be said for job plans. Planners write down the steps a mechanic or technician will need to take to successfully complete the task they are assigned. But a job plan needs to be written in a way that builds trust between what the Planner envisioned needing to be done and how the mechanic understood the message.3 If the Planner takes short cuts in the job plans and work details, technicians will begin to overlook the work details and eventually fail to do the task at hand. This can lead to premature failure, bad quality in your product, or injure someone.
3. Learn how to say No. But also learn to negotiate.
This one should be number one in my opinion. The work place can be a minefield of office politics, unknown agendas, and half truths. OR... the work place can be some where you communicate openly, people are held accountable, and project agendas are shared. Actually I bet you work somewhere in between those two extremes. But the one thing we can do to shift things for the better is to be honest about the limits we have in our day and just say no. Too many times we say yes just to appease the person in front of us or on the phone, when you know deep down there is no way we can keep the commitment you just made. The compromise to work towards is not a flat out NO, but respond back with "No, not now, but when?" No, I can't do what you're asking of me right this minute, but here's what I can do and how does that work with your schedule.4 This type of communication opens the door to negotiating what you can get done, when someone really needs it done, and what we might have to change to meet everyone's needs.
4. Respect your team members
People drawn to a career in maintenance and reliability have a uniqueness about themselves. They are generally a technically minded person who understands the intricacies of equipment and processes. They are also generally not afraid to tell that you are wrong, why they are right, and why whoever worked on this piece of equipment last should be fired. 5 The challenge is that maintenance personnel are hard wired to think a certain way and don't always realize there are others that don't see the world with same perspective. We spend 8-10 hours a day, 5 days a week with our team members. There's some weeks where you will literally see the people at work more than you do your family and friends. So what kind of work place do we want to come to if we can't show respect to what is essentially your second family? 6 This one will probably take more practice and patience to adopt than any of the other rules. Why? We're not trying to change the way they think or act, but we're trying to open someone else's eyes to a new perspective on the world. That kind of change takes time to take root.
5. Enhance an implementation. Do not criticize it.
Rarely do we get to into a greenfield plant and layout the framework for a brand new maintenance program. Normally we come to a company that has an established department with its own set of policies and procedures. The least effective thing we can do is sit around and complain about how crazy the inventory restocking policy is. If its that crazy, take a few minutes to look at what could be changed. Look at what or how the department, or company, gain from making changes to the process. Does it increase work record accuracy? Does it minimize the number of purchases orders issued in a week? Does it make the department personnel less anxious about their jobs? Presenting an idea that enhances a existing procedure shows we're willing to adapt and build on the existing structure, not tear down or denigrate what others have done before you.
So what changes are you going to try to make in your department?
-
My apologies to everyone named Bob. Maybe Sam looked at instead. ↩
-
But it's getting more and more common these days. ↩
-
If the plant is down, it's down and you get to it. But if the plant is down everytime they come to you... you've got bigger problems to worry about. ↩
-
Generally speaking of course. ↩
-
We don't always get to pick our family members, but we can chose how we treat them. ↩